10 Advanced Ways to Extend the Lifespan of Your Power Tools
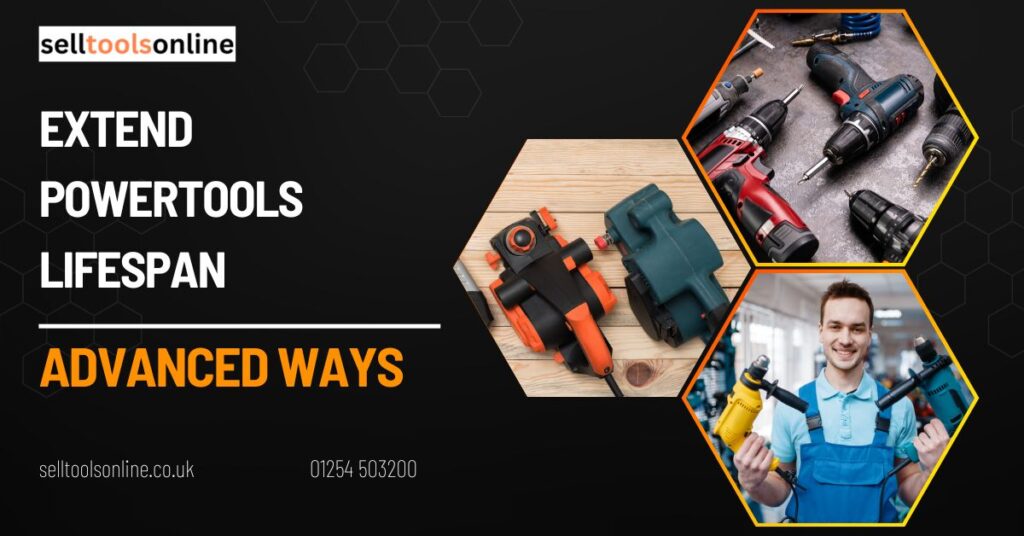
As a tradesman, your power tools are crucial to your livelihood. Regular maintenance is essential to prevent costly repairs, reduce downtime, and boost productivity. By incorporating advanced techniques into your routine, you can significantly extend the lifespan of your tools and save up to £1,500 annually, as estimated by industry reports.
This guide outlines 10 expert tips to help you optimise your power tool maintenance, covering thermal management, performance enhancement, and smart storage solutions. Whether you’re a contractor, builder, electrician, or plumber, these practical strategies will enable you to:
- Prolong tool lifespan
- Minimise repair costs
- Maximise efficiency
Let’s dive into the advanced methods to keep your power tools in top condition.
10 Ways to Extend the Lifespan of Your Power Tools
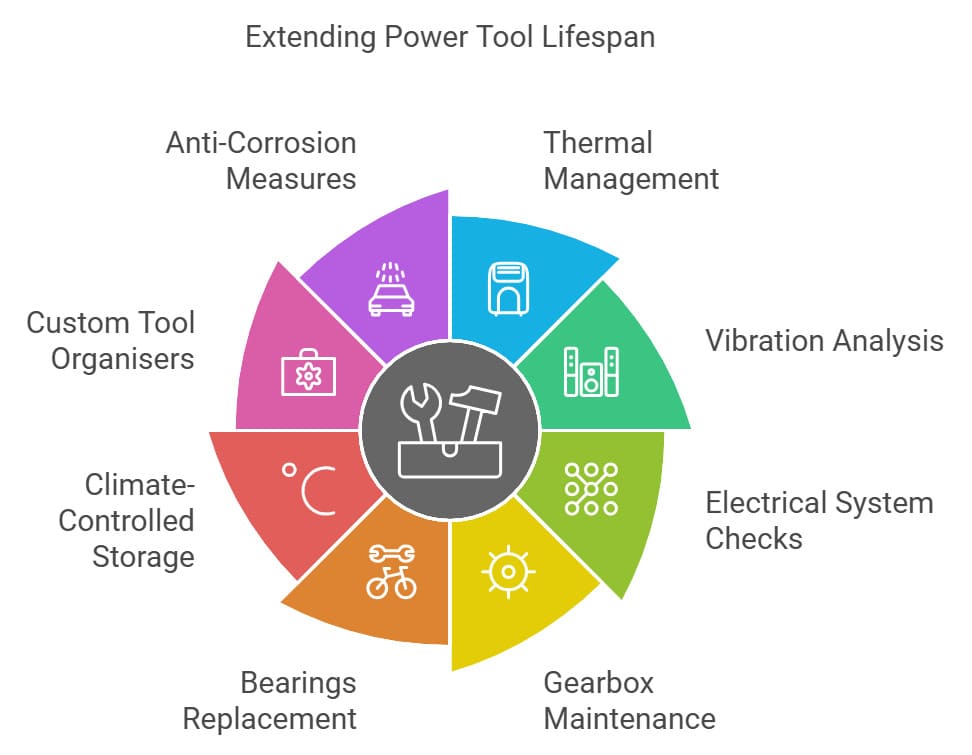
Advanced Maintenance Techniques (1-5)
Implementing these advanced maintenance techniques will help prevent premature wear, reduce breakdowns, and extend the lifespan of your power tools.
1. Thermal Management: Preventing Overheating
Overheating is a common culprit behind power tool failure. Prolonged exposure to high temperatures can damage motor windings, reduce efficiency, and compromise tool reliability. To mitigate this:
- Utilise thermal imaging cameras to detect heat buildup and identify potential hotspots
- Fit heat sinks or cooling fins to dissipate heat and improve airflow
- Regularly clean tools to prevent dust accumulation, which can exacerbate overheating
- Ensure proper ventilation in workshops and storage areas
2. Vibration Analysis: Identifying Imbalance Issues
Vibration analysis helps detect imbalance or bearing wear issues that can lead to premature tool failure. By using:
- Vibration analysis tools, you can identify anomalies and schedule maintenance
- Balancing services for rotating components, such as drill bits and saw blades
- Regular inspection of bearings and mounts to detect signs of wear
3. Electrical System Checks: Ensuring Safety and Reliability
Electrical system faults can compromise tool performance and safety. Conduct:
- Regular inspections of cords, plugs, and switches to detect damage or wear
- Cleaning of electrical contacts and components to prevent corrosion
- Testing of earth continuity and insulation resistance to ensure electrical safety
- Visual checks for signs of overheating, such as discolouration or melting
4. Gearbox Maintenance: Smooth Operation
Gearbox maintenance ensures smooth operation and prevents damage. Perform:
- Regular cleaning and lubrication of gears to reduce friction and wear
- Inspection of gear teeth and bearings to detect signs of wear
- Adjustment of gearbox tension and alignment to maintain optimal performance
- Replacement of worn or damaged gearbox components
5. Bearings Replacement: Upgrade to High-Quality Bearings
Upgrading to high-quality bearings reduces wear and tear. Consider:
- Replacing bearings every 500-1000 hours, depending on tool usage and manufacturer guidelines
- Using bearings with improved load-carrying capacity and corrosion resistance
- Consulting manufacturer guidelines for replacement and selecting compatible bearings
Read More: 10 Tips to Quickly Sell Your Tools Online
Smart Storage and Handling (6-8)
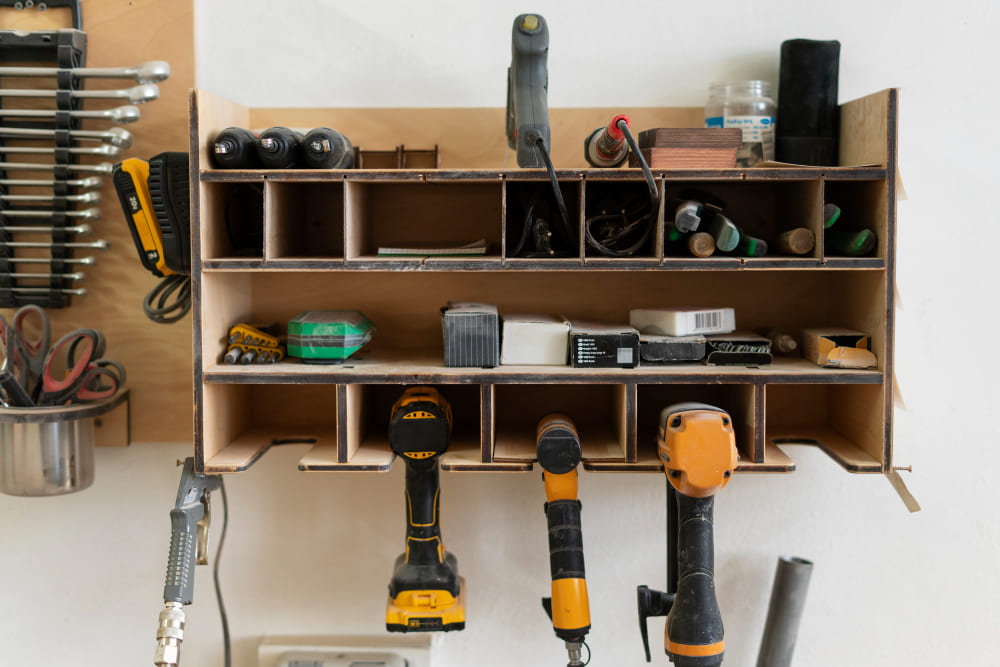
Proper storage and handling techniques are crucial to minimising wear and tear on your power tools, reducing downtime, and prolonging lifespan.
6. Climate-Controlled Storage: Mitigating Environmental Factors
Environmental factors can significantly impact tool longevity. Store tools in a controlled environment to:
- Maintain a consistent temperature range (10-20°C/50-68°F) to prevent thermal shock and contraction
- Regulate humidity levels (40-60%) to minimise corrosion, moisture damage, and rust
- Protect tools from direct sunlight, which can cause UV degradation, discoloration, and plastic component brittleness
- Position storage areas away from areas prone to flooding, excessive moisture, or high humidity
Consider investing in:
- Climate-controlled storage cabinets or containers
- Desiccant packets or silica gel to maintain dry conditions
- Thermometers and hygrometers to monitor storage conditions
7. Custom Tool Organisers: Efficient Storage and Protection
Custom organisers safeguard tools, reduce clutter, and optimise workshop efficiency. Design and build organisers to:
- Minimise tool movement and vibration, reducing wear and tear on components
- Protect against dust, debris, and contaminants that can compromise tool performance
- Ensure easy access and visibility, reducing retrieval time and enhancing productivity
- Utilise durable materials, such as steel, heavy-duty plastic, or hardwood
Consider incorporating:
- Adjustable dividers and compartments for tailored storage
- Soft-close drawers and doors to prevent tool damage
- Labelled storage for easy identification and inventory management
8. Anti-Corrosion Measures: Safeguarding Metal Components
Apply rust inhibitors and protective coatings to safeguard metal components from corrosion:
- Utilise rust-inhibiting sprays, wipes, or dips on tool bodies and fittings
- Apply protective coatings, such as zinc or ceramic, to high-wear areas
- Regularly inspect and reapply coatings as needed to maintain protection
- Store tools in dry, well-ventilated areas to prevent moisture accumulation
Consider using:
- VCI (Vapour Corrosion Inhibitor) bags or packaging materials
- Desiccant packets or silica gel to maintain dry storage conditions
- Corrosion-resistant materials for tool storage and handling equipment
Read More: How to Clean and Restore Old Tools Before Selling
Performance Optimization (9-10)
Optimizing your power tools’ performance ensures they operate efficiently, effectively, and safely.
9. Motor Tuning: Enhancing Efficiency and Reliability
Motor tuning optimizes performance, reduces energy consumption, and prolongs lifespan:
- Consult manufacturer guidelines for motor tuning specifications
- Adjust motor settings to match workload demands
- Upgrade to high-efficiency motors or ESC (Electronic Speed Control) systems
- Regularly inspect and maintain motor components, such as brushes and bearings
Consider:
- Using motor testing equipment to identify performance issues
- Implementing a regular maintenance schedule for motor servicing
- Upgrading to energy-efficient motors with reduced power consumption
10. Accessories and Attachment Maintenance: Maximizing Performance
Proper maintenance of accessories and attachments ensures optimal performance:
- Regularly inspect and clean drill bits, saw blades, and other attachments
- Sharpen or replace worn or damaged cutting edges
- Lubricate moving parts and hinges to reduce friction
- Store accessories and attachments in designated, protective cases
Consider:
- Using manufacturer-recommended cleaning solutions and maintenance products
- Implementing a colour-coding system for easy accessory identification
- Scheduling regular maintenance for frequently used attachments
By implementing these 10 advanced techniques, you’ll significantly extend the lifespan of your power tools, reduce maintenance costs, and enhance productivity. Remember to consult manufacturer guidelines and industry publications.
If you’re thinking of upgrading or clearing out your tool collection, why not sell your unwanted tools to Sell Tools Online? We buy used or new branded hand, power, and air tools for cash, with payment made within 24 hours.